مسكن
>
working process of ball milling
منتج
أكثر من 30 نوعًا من المنتجات تغطي التعدين وسحق البناء والطحن الصناعي ومواد البناء الخضراء وغيرها من المجالات
working process of ball milling
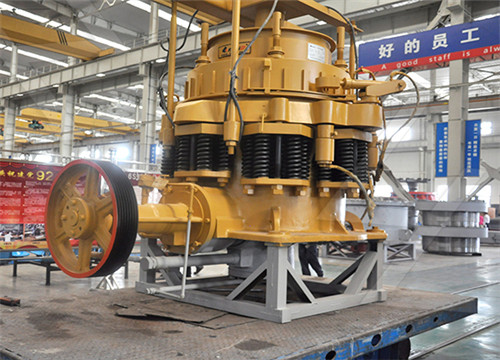
Ball Mill ScienceDirect
The ball milling process is carried out for approximately 100–150 h to obtain uniform-sized fine powder. In high-energy ball milling, vacuum or a specific gaseous atmosphere is maintained inside the chamber. High-energy mills are classified into attrition ball mills, Abstract. Ball milling is a simple, fast, cost-effective green technology with enormous potential. One of the most interesting applications of this technology in the field of Ball milling: a green technology for the preparation andThe ball-milling process is common in grinding machines as well as in reactors where various functional materials can be created by mechanochemical synthesis. A simple Ball Milling ScienceDirect
get price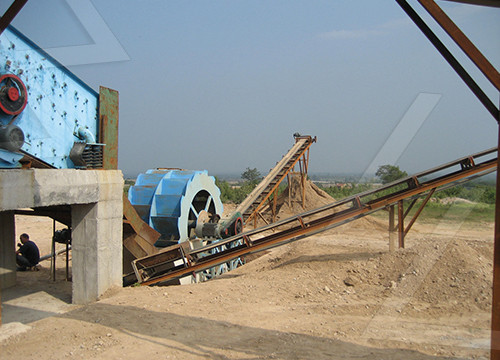
Ball milling as a mechanochemical technology for
2020年9月1日 Ball milling procedure is inexpensive and reproducible. A few studies focused on the use of ball milling to produce novel engineered biochar with enhanced 2019年5月22日 Materials Weekly. The ball mill consists of a metal cylinder and a ball. The working principle is that when the cylinder is rotated, the grinding body (ball) and the The working principle of ball mill MeetyouBall milling, a shear-force dominant process where the particle size goes on reducing by impact and attrition mainly consists of metallic balls (generally Zirconia (ZrO2) or steel Ball Milling ScienceDirect
get price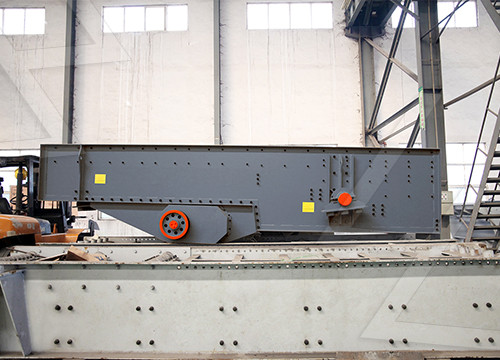
Working principle of ball milling process.
Download scientific diagram Working principle of ball milling process. from publication: Ball milling of jute fibre wastes to prepare nanocellulose The objective of this work was to use the2023年4月8日 Ball milling techniques includes the mechanical ball-milling, the reactive ball-milling, and the mechanical alloying. In general, the longer the milling time is, the smaller Investigation of ball-milling process onAmongst all the methods that can be employed for the mechano-chemical processing of cellulose, ball milling is an emerging technique, which allows avoiding organic solvents. Being easy to use, fast, economical and environmentally friendly, this technique has recently acquired growing interest in chemistry.Ball milling: a green technology for the preparation and
get price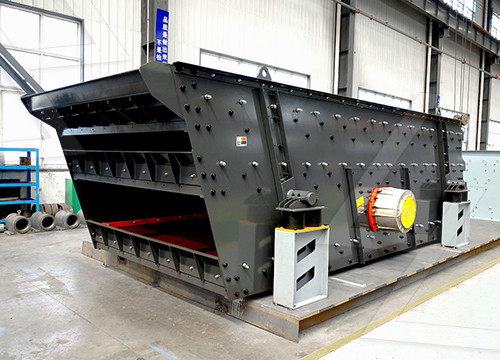
Ball Milling ScienceDirect
Ball milling, a shear-force dominant process where the particle size goes on reducing by impact and attrition mainly consists of metallic balls (generally Zirconia (ZrO2) or steel balls), acting as grinding media and rotating shell to create centrifugal force.Nanomaterials. A.S. Edelstein, in Encyclopedia of Materials: Science and Technology, 2001 1.4 Mechanical Synthesis Methods. High-energy ball milling, also called mechanical attrition, can be used to reduce the grain size of materials from many micrometers to 2–20nm (see Mechanical Alloying).This is a result of the cold-working process creating large-angle High-Energy Ball Milling ScienceDirect2021年2月19日 Metrics Abstract Taguchi-based experimental design technique has been a major research area for making systematic approaches to understand the complex process of ball mill process parameters influencing on the Comparative Study on Improving the Ball Mill Process
get price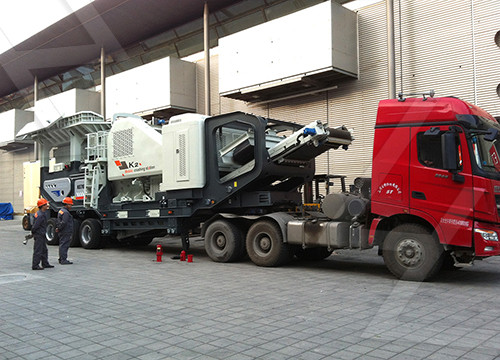
Frontiers The Effect of Ball Milling Time on Open
2021年12月14日 Ball milling technology is the classical technology to isolate representative lignin in the cell wall of biomass for further investigation.2019年2月7日 The ball mill process is very complicated process governed by many parameters, such as ball size, ball shape, ball filing, slurry loading ( with respect to ball amount), powder loading with respect to the amount of total slurry ( slurry viscosity), and rotation speed. such as the mill capacity (1 kg) and working time (12 hours) in order toDesign, Construction, and Operation of a High-Energy Mill 2020年8月28日 1 Citations Metrics Abstract To achieve the secondary production in multistage fracturing wells of tight oil, milling tools are usually used to remove the multistage fracturing ball seats to achieve production with a large diameter in later.Experimental study on the working performance of
get price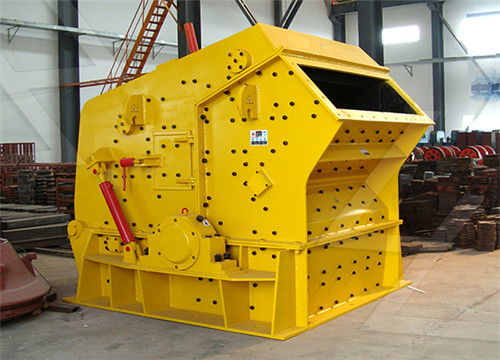
Ball Milling ScienceDirect
Ball milling, a shear-force dominant process where the particle size goes on reducing by impact and attrition mainly consists of metallic balls (generally Zirconia (ZrO2) or steel balls), acting as grinding media and rotating shell to create centrifugal force.High-energy ball milling is a mechanical deformation process that is frequently used for producing nanocrystalline metals or alloys in powder form. This technique belongs to the comminution or attrition approach introduced in Chapter 1.High-Energy Ball Milling ScienceDirect2021年2月19日 Metrics Abstract Taguchi-based experimental design technique has been a major research area for making systematic approaches to understand the complex process of ball mill process parameters influencing on the Comparative Study on Improving the Ball Mill Process
get price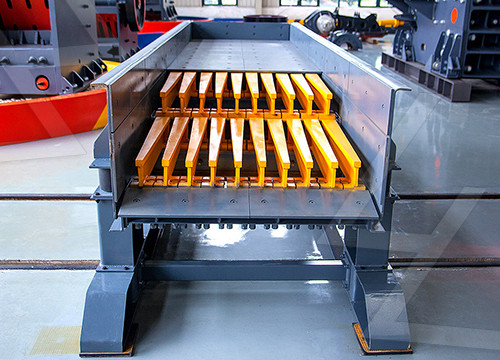
Modeling and estimation of cutting forces in ball helical
2021年8月18日 Finally, higher simulation precision of cutting force model in ball helical milling process is received. Milling forces play an important role in the milling process and are generally calculated by the mechanistic or numerical methods; reliable model of cuttin Working on a manuscript? Avoid the common mistakes2021年12月14日 Ball milling technology is the classical technology to isolate representative lignin in the cell wall of biomass for further investigation.Frontiers The Effect of Ball Milling Time on Open 2019年2月7日 The ball mill process is very complicated process governed by many parameters, such as ball size, ball shape, ball filing, slurry loading ( with respect to ball amount), powder loading with respect to the amount of total slurry ( slurry viscosity), and rotation speed. such as the mill capacity (1 kg) and working time (12 hours) in order toDesign, Construction, and Operation of a High-Energy Mill
get price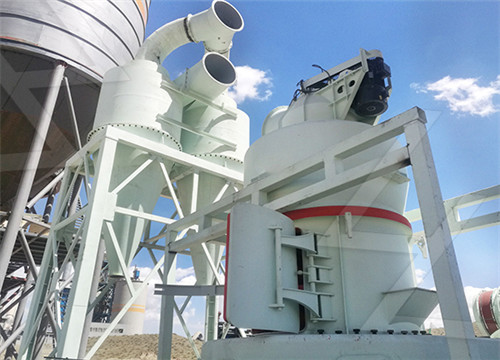
Effect of Ball Milling Mechanism on the Density and
2022年9月13日 Abstract Present work aims to improve density and hardness of Al matrix by changing rotational speed and milling time. Two mechanisms, low-speed ball milling (Lmpl) and dual speed ball milling (Dmpl) were adopted to grind Al powder. Average particle size of Al powder got reduced when the milling condition changed from Lmpl to Analysis of ball-milling process under various conditions (i.e. working volume, milling time, and material load) on the material properties (i.e. chemical composition, as well as particle size and morphology), product yield, and electricity consumption was investigated.Working Volume and Milling Time on the Product
get price